Just how to Recognize What is Porosity in Welding and Improve Your Strategy
Porosity in Welding: Identifying Common Issues and Implementing Best Practices for Prevention
Porosity in welding is a pervasive issue that often goes undetected till it causes significant problems with the honesty of welds. In this discussion, we will check out the essential factors adding to porosity formation, examine its destructive impacts on weld performance, and discuss the best practices that can be taken on to lessen porosity incident in welding procedures.
Usual Causes of Porosity

Using filthy or damp filler materials can introduce impurities into the weld, adding to porosity concerns. To reduce these common causes of porosity, thorough cleansing of base metals, appropriate securing gas selection, and adherence to ideal welding criteria are essential techniques in attaining top notch, porosity-free welds.
Effect of Porosity on Weld Top Quality

The visibility of porosity in welding can dramatically compromise the structural stability and mechanical properties of welded joints. Porosity creates gaps within the weld metal, compromising its total stamina and load-bearing capacity. These voids function as stress and anxiety focus points, making the weld more at risk to breaking and failure under applied lots. Furthermore, porosity can reduce the weld's resistance to deterioration and various other ecological factors, better lessening its long life and efficiency.
Welds with high porosity levels tend to display lower influence stamina and minimized ability to deform plastically before fracturing. Porosity can hamper the weld's ability to successfully transfer pressures, leading to early weld failing and possible security threats in important structures.
Ideal Practices for Porosity Prevention
To improve the architectural integrity and high quality of bonded joints, what specific procedures can be implemented to reduce the Read Full Report event of porosity during the welding procedure? Porosity prevention in welding is vital to ensure the honesty and strength of the final weld. One reliable technique appertains cleaning of the base steel, getting rid of any pollutants such as corrosion, oil, paint, or wetness that can result in gas entrapment. Guaranteeing that the welding devices is in great condition, with tidy consumables and appropriate gas flow rates, can additionally dramatically lower porosity. In addition, maintaining a steady arc and regulating the welding criteria, such as voltage, current, and travel speed, helps produce a constant weld swimming pool that decreases the risk of gas entrapment. Using the appropriate welding method for the certain product being bonded, such as changing the welding angle and gun placement, can additionally protect against porosity. Regular inspection of welds and instant removal of any type of problems determined during the welding process are important techniques to prevent porosity and produce top quality welds.
Relevance of Appropriate Welding Techniques
Applying correct welding strategies is extremely important in making certain the architectural integrity and high quality of bonded joints, building upon the structure of find out reliable porosity avoidance steps. Extreme heat can lead to increased porosity due to the entrapment of gases in the weld pool. In addition, using the proper welding parameters, such as voltage, present, and travel rate, is critical for attaining sound welds with very little porosity.
In addition, the choice of welding process, whether it be MIG, TIG, or stick welding, must straighten with the specific needs of the job to guarantee optimal outcomes. Correct cleansing and preparation of the base metal, as well as choosing the best filler product, are likewise vital parts of efficient welding strategies. By sticking to these finest techniques, welders can minimize the risk of porosity formation and produce premium, structurally audio welds.
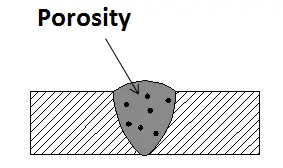
Examining and Quality Assurance Procedures
Evaluating procedures are vital to find and stop porosity in welding, guaranteeing the toughness and sturdiness of the last item. Non-destructive screening techniques such as ultrasonic testing, radiographic testing, and visual inspection are commonly used to recognize possible flaws like porosity.
Carrying out pre-weld and post-weld evaluations is additionally important in preserving quality assurance criteria. Pre-weld assessments involve validating the materials, equipment setups, and sanitation of the workplace to stop contamination. Post-weld assessments, on the other hand, evaluate the last weld for any flaws, including porosity, and verify that it meets defined standards. Applying an extensive quality assurance plan that the original source consists of comprehensive screening treatments and evaluations is extremely important to decreasing porosity concerns and ensuring the general quality of welded joints.
Verdict
Finally, porosity in welding can be a typical problem that influences the top quality of welds. By recognizing the common causes of porosity and implementing best methods for avoidance, such as correct welding strategies and screening measures, welders can guarantee high quality and trustworthy welds. It is crucial to prioritize prevention methods to decrease the occurrence of porosity and keep the honesty of bonded frameworks.